In many cases pipe vibration are a consequence of a mechanical amplification due to a natural frequency of a pipe segment between its supports.
Discharge pipe bends of hyper compressors are often affected by this mechanism.
A typical approach for a mitigation would be the increase in stiffness for example by means of additional supports.
This approach can imply huge engineering efforts when a pipe stress analysis needs to be included.
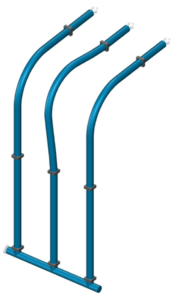
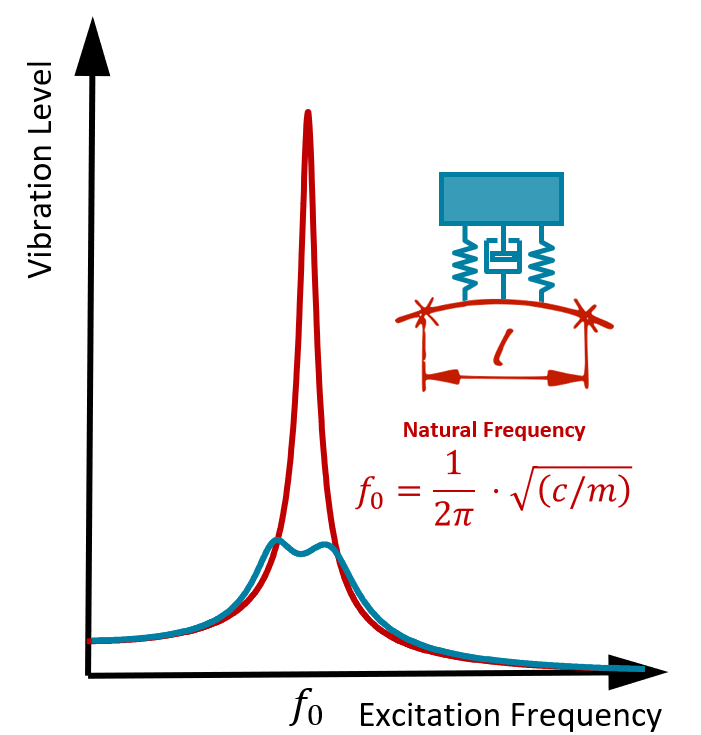
A tuned mass dampener is able to modify the vibration behavior significantly without the application of further constraints to the pipe.
It consists of a mass, a spring and a damping mechanism and it is attached to the vibrating pipe. It almost completely eliminates the resonance amplification at resonance.
This is why we call it a “Dynamic Pipe Support”.
The design of a tuned mass absorber needs to allow a flexible tuning of the dynamic properties.
The concept of our Dynamic Pipe Supports (DPS) gives us the opportunity to solve resonance based vibration issues immediately during the root cause analysis on site.
Therefore, the dynamic properties for the absorber stiffness and damping ratios can be easily adjusted on site.
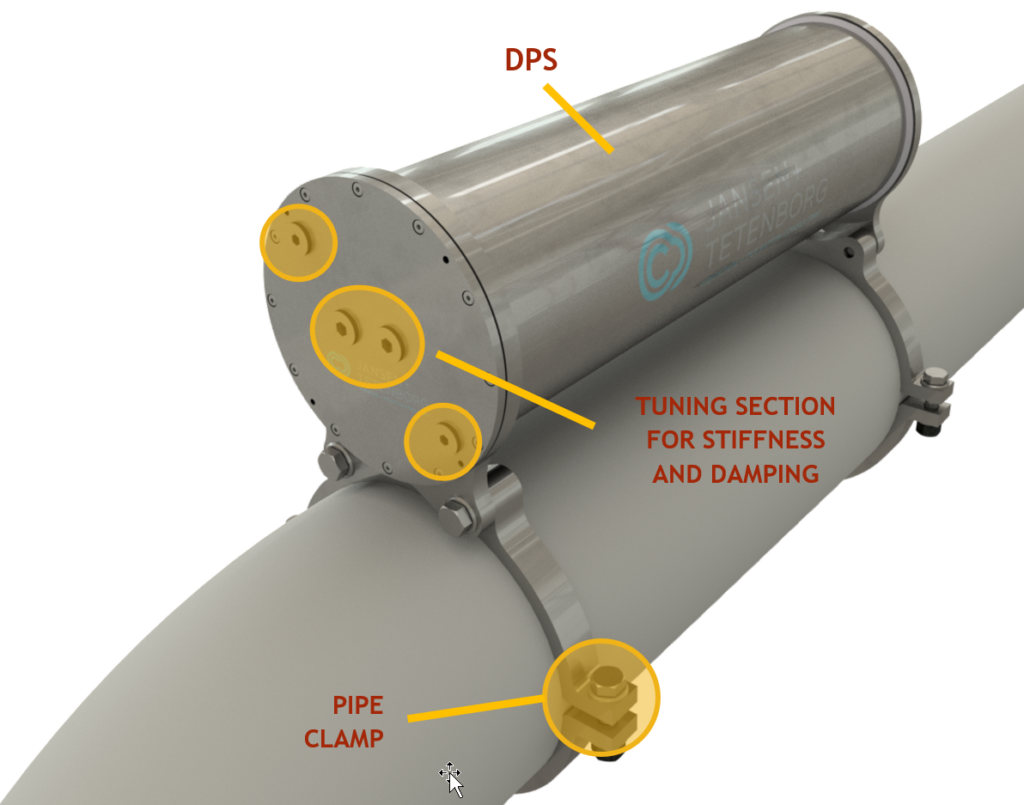
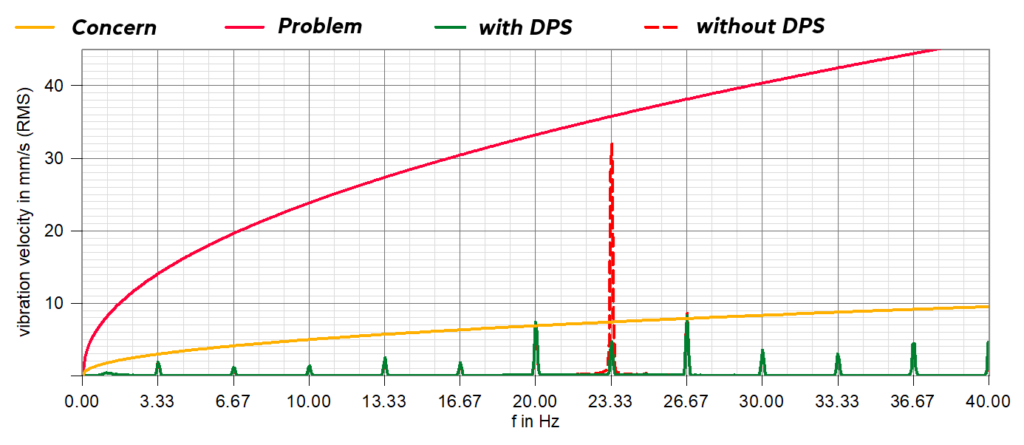
The absorber mass itself has been quantified to fit for all typical piping sections in common compressor plants. Thus, the DPS offers a great vibration reduction potential to the operator.
The presented vibration spectrum belongs to a K10 discharge pipe bend with and without a Dynamic Pipe Support. The Dynamic Pipe Support is capable to reduce the vibration level at resonance down to the strict vibration guidance values of the Energy Institute “Guidelines for the avoidance of fatigue failure in process pipework”.
A tuned mass dampener is a perfect mitigation measure for bending vibrations of pipes in resonance.
We will be happy to give a demonstration of the technology at your facility. Please do not hesitate to get in contact.